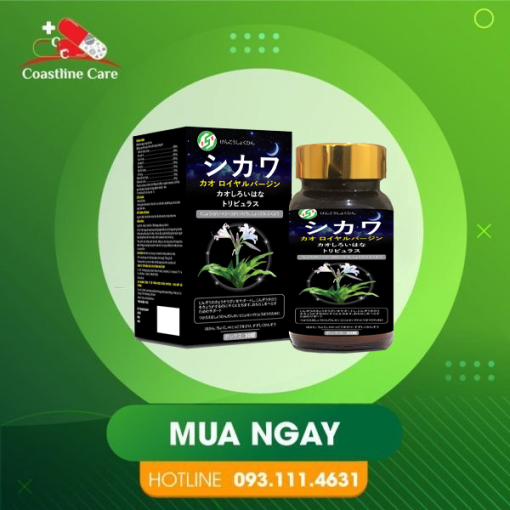
Once you have selected your critical classes, it is possible to commence brainstorming probable will cause for each. Take into consideration all of the things that can influence your procedure or item and Observe them down as probable results in.
These diagrams are helpful for product or service builders when new merchandise are now being created. This also can help teams identify which sources will probably be desired at unique instances to establish quality Handle challenges right before they occur.
Consequently smaller issues may be provided more notice than they want and enormous ones not enough. For the reason that much in the diagram's inputs and interpretations are subjective, it could also bring on disagreements amongst administrators who perspective the chart from different perspectives.
Right after graduating, Ishikawa to begin with served within the Japanese Navy as a technological officer. His duties provided focusing on chemical weapons and gasoline generation, roles that honed his abilities in systematic Examination and system Manage.
The Ishikawa diagram was produced by Kaoru Ishikawa through the 1960s as a technique for measuring good quality Manage procedures during the shipbuilding industry.
Technique/Procedure – This refers back to the solutions and treatments applied to create or provide the service or product.
Likely triggers that do circuitously make clear the failure, but theoretically might have triggered it, could be detailed inside the Ishikawa. This guarantees they will not be forgotten; on the other hand, improved explanations really should be prioritized for investigation.
One of many humanoid species that wears silver armor and carries a pink pouch. Ponchette no Yoroi-san's pouch was created by himself, and "Chiikawa originally tried to purchase it at his marketplace, however it turned out it had nha thuoc tay a leaking gap, so just after Hachiware pointed it out, he gave Chiikawa a completely new pouch".
Good quality circles normally include a small group of workforce within the very same operate location who satisfy often to detect, analyze, and resolve operate-associated troubles. The method includes:
Each individual cause or reason for imperfection is really a source of variation. Leads to are often grouped into significant categories to identify and classify these sources of variation.
There might be a threat of concentrating also closely on personal things in place of contemplating how they could communicate with nha thuoc tay one another.
Produce the trouble assertion at the Centre-suitable with the flipchart or whiteboard, box it, and attract a horizontal arrow managing to it.
Once you have a listing of feasible will cause, it is helpful to type and prioritize them based on their chance of getting nha thuoc tay root causes.
Other widespread employs of your Ishikawa diagram include making use of it for a methodology for creating solution types that clear up practical issues. It can be Utilized in excellent defect avoidance to detect possible elements leading to an Total influence.